Molla Builders is a full-service residential remodeling company that focuses on interior renovations, including kitchens, bathrooms and basements. In his early days as a builder, Dennis Molla used fiberglass insulation on remodeling projects, but these days, he chooses ROCKWOOL for its superior thermal performance, moisture resistance and fire resilience. In fact, when his local distributor stopped carrying ROCKWOOL insulation, he drove out of his way to keep using the product. Building with high-quality materials that go beyond code for lasting performance has been key to growing his reputation — and his business.
Dennis used ROCKWOOL stone wool insulation for this 1960s split-level home energy retrofit in Peabody, Massachusetts, with a vapor-open system on the lower level against the foundation to help reduce moisture buildup and maximize drying potential. In this climate zone, thermal performance is a primary driver for using stone wool because the temperatures can range from 100 F in the summer with high humidity to below zero during the colder months.
Building a durable home that stands the test of time was especially important on this remodel, as his brother-in-law is the homeowner, and the plan is to raise a family there in the future.
“The insulation was horrible in this house,” Dennis says. “It was batt insulation and pretty much disintegrated when pulling everything out.” Moisture damage due to poor-quality insulation products or installation methods is an issue Dennis sees frequently with his remodeling projects in the area. When it comes to water leaks, he says it isn’t a matter of if but a matter of when.
“As we’re pulling back rotted-out plywood, that old insulation is just soaked. It does not dry out. All that moisture keeps spreading to the lumber,” he adds. “We’ve had so many instances where we just end up replacing the whole side of the house.”
This renovation project involved a full gut of the kitchen, bathrooms and bedrooms and finishing the basement to provide additional living space. The goal was to improve thermal and acoustic performance to create a more comfortable, energy-efficient home.
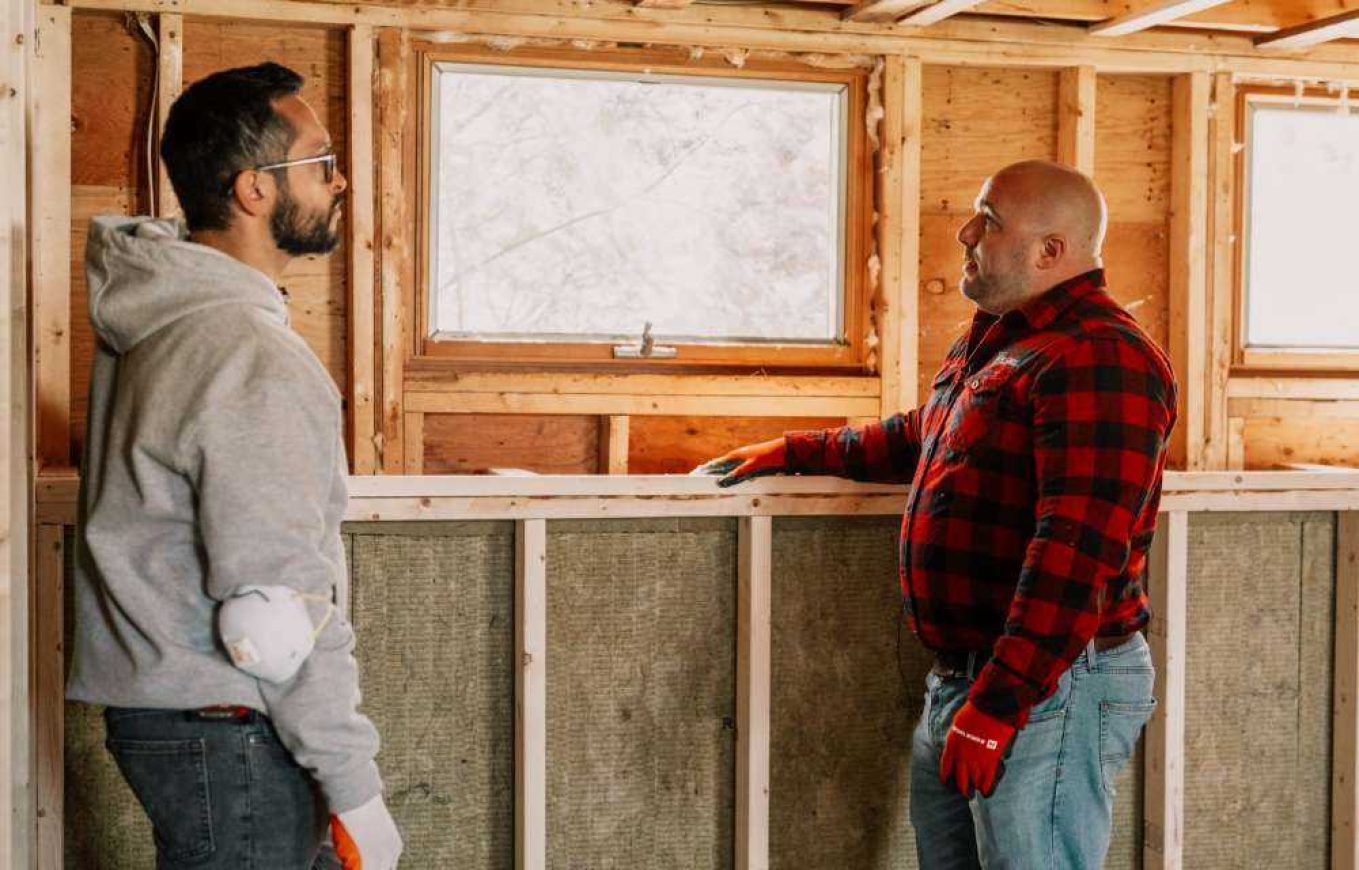
Dennis used 1.5" of ROCKWOOL Comfortboard® 80 in the basement against the exposed foundation with ROCKWOOL Comfortbatt® R-15 on top and finished with a smart vapor retarder on the lower level of the home. Since this is a basement wall and below grade, the primary drying would be toward the interior, as typically the soil moisture level is higher. Thus, the smart vapor retarder, installed as an air barrier, will allow the assembly to dry to the interior while it controls the risk of condensation over the cold interior surface of the basement wall that could occur due to vapor diffusion or air leakage.
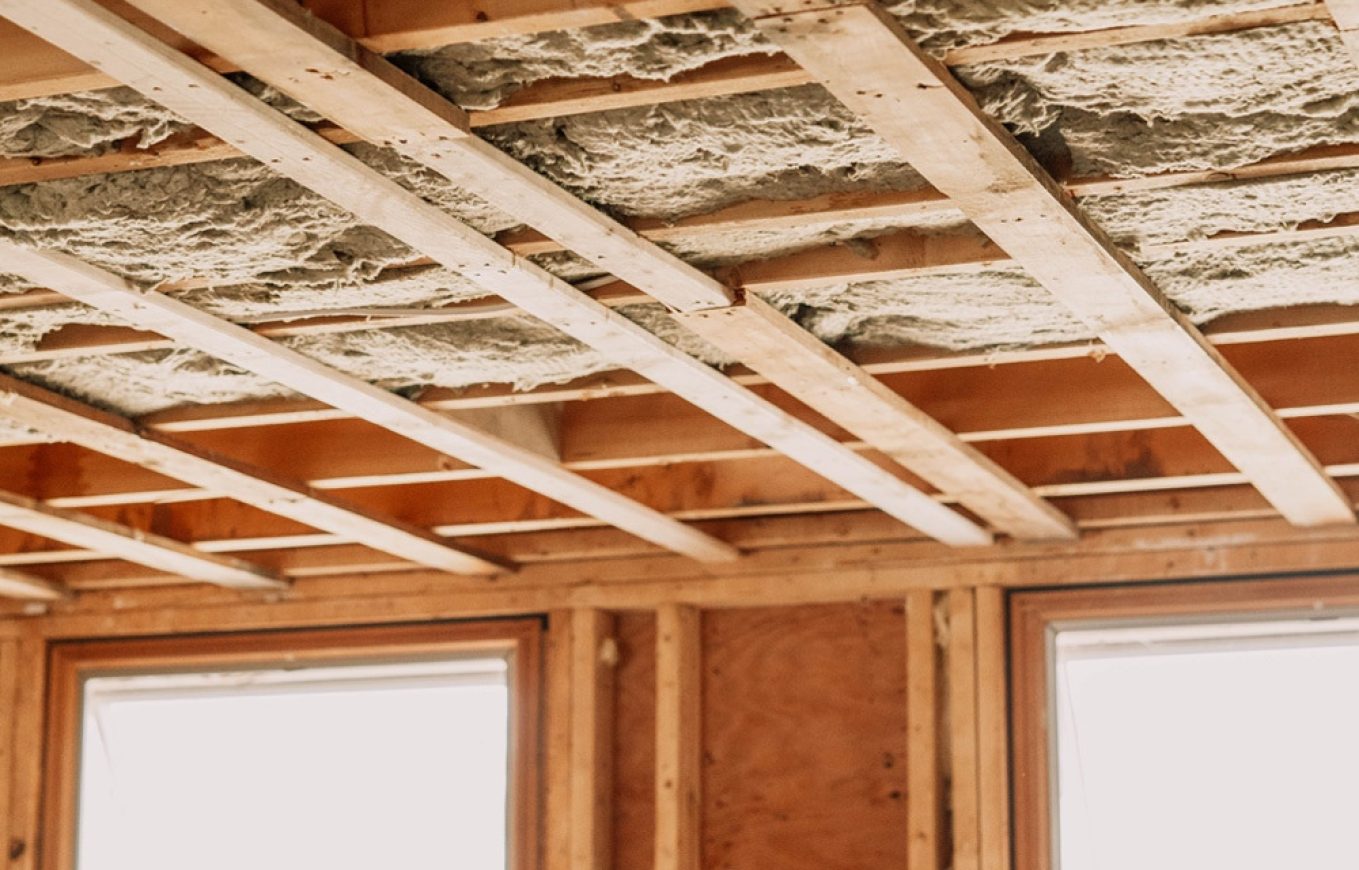
ROCKWOOL Safe'n'Sound 6" was used for the ceilings and 3" for the interior walls to isolate noise and improve acoustic comfort. Since the plan is to turn one area on the lower level into a drum room, soundproofing was a huge priority for the homeowners.
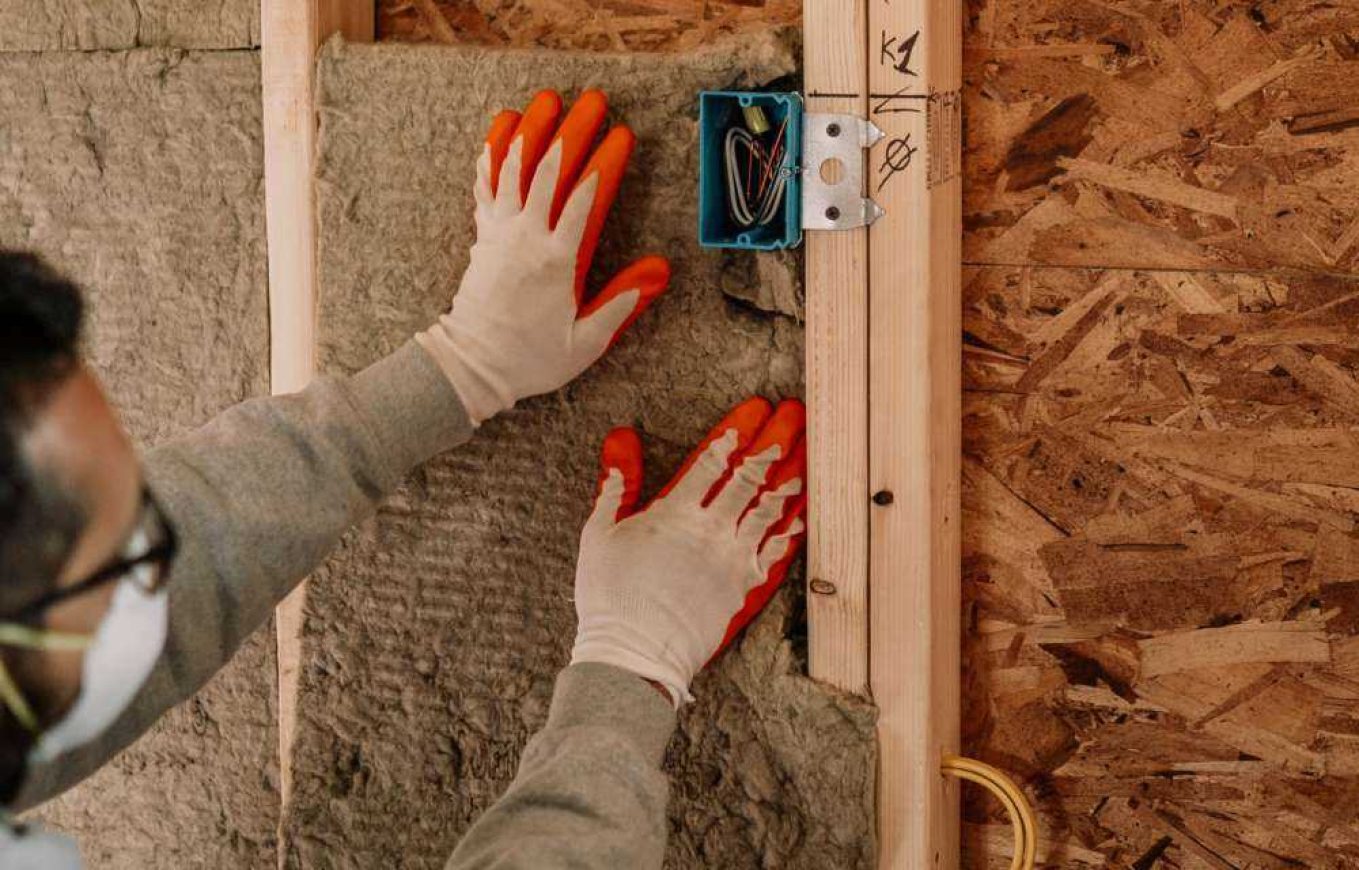
ROCKWOOL Comfortbatt was also used extensively in the exterior assembly to achieve R-15 in the two-by-four walls. It was important for Dennis to do an effective job of detailing around outlet boxes and wires to maintain the effective R-value, as even missing a small portion of these areas could result in a loss of up to 50% of the R-value for the whole wall.
R‑Class has been very beneficial. When we have any questions, we can reach out to the technical team and get the answers we need.– Dennis Molla
Molla Builders sees great value in joining the R‑Class™ program, and Dennis appreciates having access to high-performance building experts and educational webinars, gaining knowledge he can use to grow his business. “R‑Class has been very beneficial. When we have any questions, we can reach out to the technical team and get the answers we need. It really makes things easier and simplifies things for us. R‑Class brings us into a community of high-performance builders who share our vision,” he adds.
The Build
- 1960s deep energy retrofit
- Molla Builders
- Peabody, Massachusetts: climate zone 5A
- Approx. 1,900 ft2
Basement
- 10" concrete foundation wall
- 1.5" ROCKWOOL Comfortboard 80 R-6.3
- 3.5" ROCKWOOL Comfortbatt R-15 between 2" × 4" wood studs 16" o.c.
- SIGA Majrex® 200 smart vapor retarder, installed as an air barrier
- 1/2" gypsum board
Exterior Walls
- Vinyl siding
- Water-resistive barrier
- 1/2" CDX plywood sheathing
- 3.5" ROCKWOOL Comfortbatt R-15 between 2" × 4" wood studs 16" o.c.
- SIGA Majrex 200 smart vapor retarder
- Blueboard and veneer plaster interior finish
Interior Walls
- Blueboard and veneer plaster interior finish
- 3" ROCKWOOL Safe'n'Sound between 2" × 4" wood studs 16" o.c.
- Blueboard and veneer plaster interior finish
Floors/Ceilings
- 3/4" oak hardwood
- 1/2" CDX plywood
- 6" ROCKWOOL Safe'n'Sound between joists
- Blueboard and veneer plaster
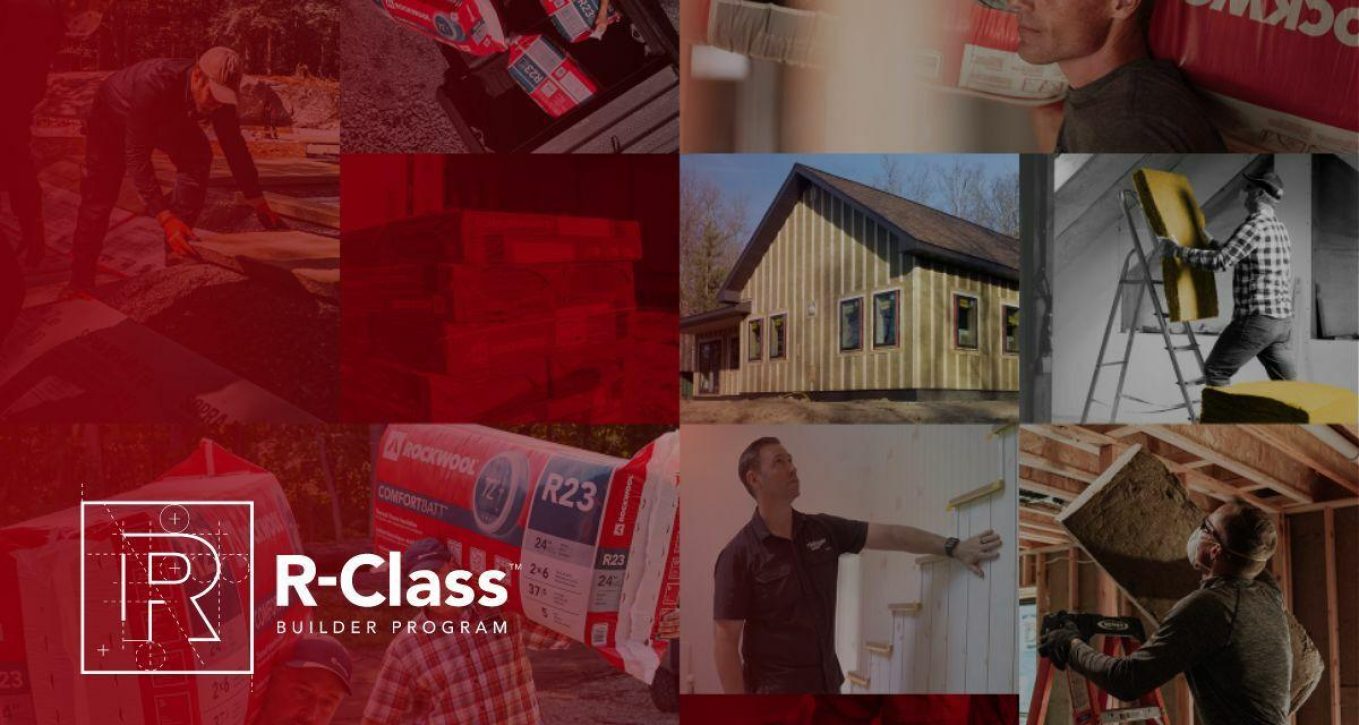
Join our R‑Class Builder Program today
Learn more about ROCKWOOL stone wool and high-performance building techniques from our experts, watch recorded R‑Class Roundtables and connect with like-minded builders who share your passion for building science.